Aluminum Extrusions
Star Extruded Shapes, Inc. is a full service aluminum extrusions provider. Not only do we extrude, we also provide aluminum fabrication, powder coating, assembly, and other finishing services. At Star, we pride ourselves in our ability to provide turnkey solutions for all of your aluminum extrusion needs.
Aluminum Extrusion Benefits
Aluminum Extrusion Capabilities
We offer a wide range of aluminum extrusion services while preserving ISO 9001:2015 certifications across all of our manufacturing facilities. Our 350,000-square-foot extrusion plant features four aluminum extrusion presses (6”, 2 – 7” & 9″ inch diameter), allowing us to service many industries and their unique needs. The versatility of presses available provides Star the unmatched ability to manufacture profiles of all different sizes.
Aluminum Extrusions Process and Design
The aluminum extrusion process involves heating the raw material (billet) and the tooling (die) simultaneously. The die is loaded into the press where the billet is then pushed through the die to form the shape. Once extruded, the material is cooled, stretched and then cut to size at the extrusion press. The material then gets transferred and staged for the tempering process – a process that uses a heat treat oven to achieve the desired hardness required. From there, the parts will either get packed for shipment or sent to our fabrication or powder coat assemblies for final fabrication or finish required.
Our experienced staff of engineers are ready to assist you with your design needs. Using the most advanced software applications, including computer-aided design (CAD) and computer-aided manufacturing (CAM) programs, we can help you design the extrusion that will work best for your application.
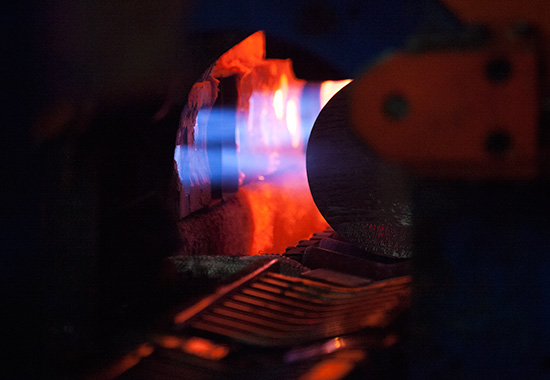
Aluminum Extrusion Services
Project Planning starts with the RFQ stage
Star conducts a feasibility review for all profile & fabrication specifications supplied by our customers. This process determines best design options, run rates, capacity analysis and identifies any areas requiring further discussion. Upon receipt of tooling orders, we follow a thorough print approval and our Product Launch Coordinator oversees new jobs from start through sample approval
To aid our customers who are working to prove out a design or process, Star has the in-house capability for supplying prototypes, short run test samples and less-than-minimum initial run sizes.