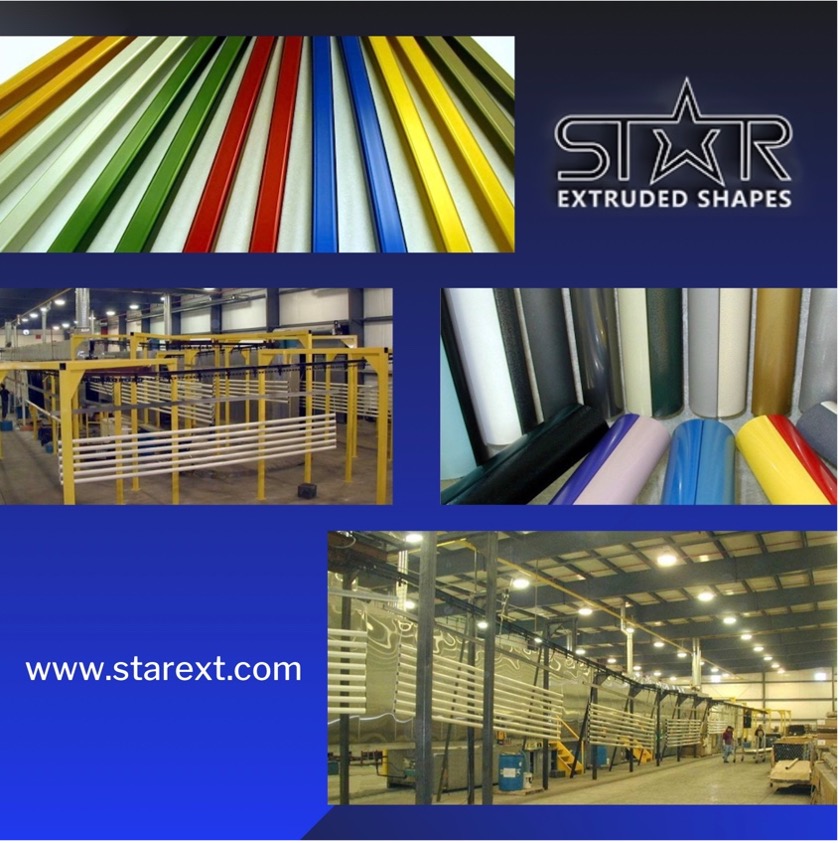
Aluminum finishing services provide a range of finishes that can improve aluminum products’ appearance, durability, and functionality. Different finishes are available to meet each application’s specific needs. These services can help protect aluminum products from corrosion, wear, and other types of damage. Additionally, aluminum finishing services can enhance the aesthetic appeal of products, making them more attractive to customers and helping to differentiate them from competitors.
Aluminum Finishing Services at Star Extruded Shapes, Inc.
Star Extruded Shapes has been in the powder coating business for 30+ years, using special coatings that are safe for the environment with a unique process that helps prevent rust and corrosion. Whether you need a coating for practical or aesthetic reasons, Star can help you find the right one.
Finishing Processes
Two of the most popular finishing processes are powder coating and anodizing. Powder coating involves electrostatically applying dry paint powder onto an extrusion baked in an oven, creating a smooth, even, durable film that protects against corrosion. Anodizing is a highly effective chemical finishing process that involves adding a protective layer to an extruded component, enhancing its durability and final appearance.
If you want to give your aluminum products a sleek and polished look, consider these two finishing processes to elevate their appearance.
A Quick Guide to Powder Coating: From Preparation to Finished Product
The powder coating process involves electrostatically spraying dry paint powder onto an extrusion. This method differs from traditional liquid paint as it is much more durable and does not require a solvent. The powder is applied using specialized equipment that charges the particles, which then adhere to the extrusion. Next, once the powder is applied, the extrusion is baked in an oven at a high temperature, causing the powder particles to melt into a liquid state.
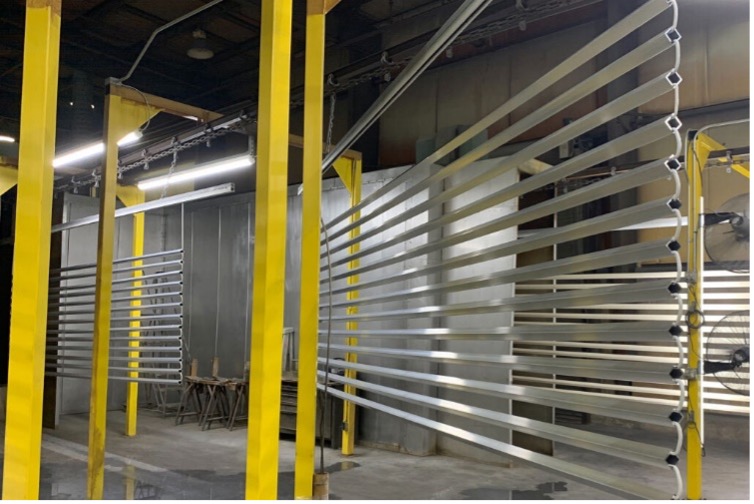
This results in particles fusing to form a smooth, even film without any runs or sags. The baking process also ensures that the film is solid and durable, providing excellent protection against corrosion and other environmental factors. Powder coating offers a versatile solution for numerous applications with its availability in various colors and finishes.
Optimizing Aluminum Extrusion Surface Preparation for Enhanced Performance
Before aluminum extrusions can be used, they are carefully cleaned to ensure quality and durability. This procedure utilizes chemicals and processes to remove surface dirt, oil, and other things. It’s essential to do this step well to ensure the extrusions are finished correctly and don’t flake or get damaged.
The Process of Powder Coating Application
Powder coating is a popular method of coating extrusion with colored pigment and resin. The process involves using an electrostatic spray gun that applies a positive charge to the powder particles, making them bond with an electrically grounded extrusion. Besides electrostatic spray guns, other powder coating methods include electrostatic spray guns, magnetic brushes, electrostatic discs, and fluidized beds.
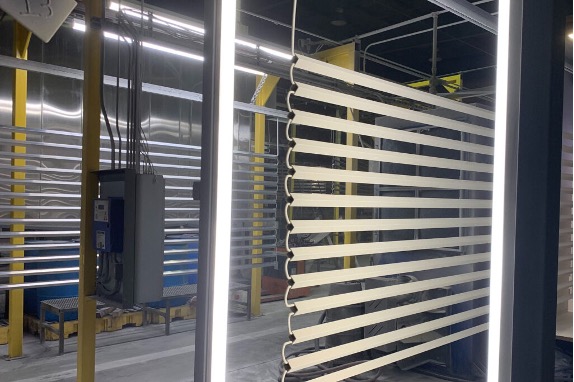
Enriching the Quality of Extruded Products
To create a durable and long-lasting coating, the extrusions undergo a baking process in a large curing oven set to a specific temperature and duration. During this process, the powder coating material is melted uniformly. After it cools down, it forms a complex and smooth coating that adheres perfectly to the surface of the extruded material. This baking process is crucial to achieving a consistent and durable coating that withstands harsh environmental conditions and provides excellent corrosion resistance.
Anodizing
Anodizing is a chemical finishing process that involves adding a protective layer to an extruded component to enhance its durability and final appearance. Specifically, the process safeguards aluminum from external elements and significantly increases its resistance to corrosion and abrasion. The Star facility offers a diverse range of anodizing specifications to cater to the specific needs of various extrusion applications. Star’s anodizing services provide long-lasting protection and a superior finish to your extruded components, ensuring their longevity and optimal performance.
Types of anodizing available include standard, two-step, double etch, and hard coat, with various options such as satin clear, black, bronze, and clear and black hard coat.
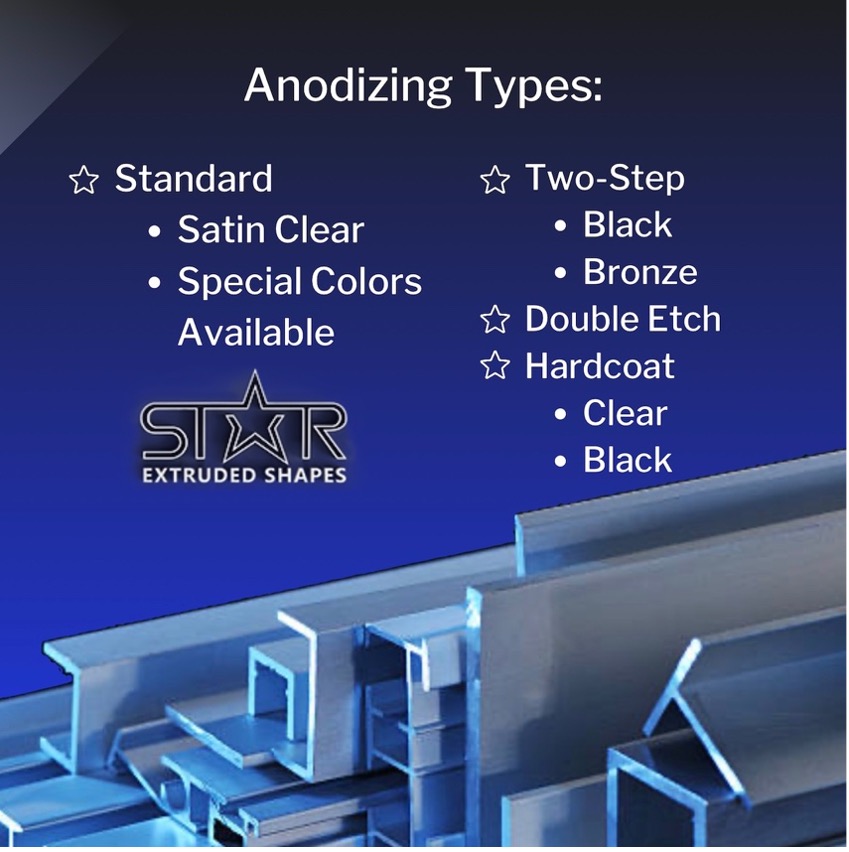
The Leading Powder Coating Services for Aluminum Extrusion
If you are wondering about the type of finishing required for your aluminum extrusion, Star Extruded Shapes can help you make an informed decision thorough expert understanding of the various finishing options available and how they can affect the surface of your product. Star’s powder coat and anodized finishing processes are comprehensive and precise, ensuring that your aluminum extrusion is not only aesthetically pleasing, but also durable and long-lasting.
Superior Finishing: Painting, Anodizing, and More
Known for proficiency in aluminum extrusion, anodizing, and painting, Star Extruded Shapes is recognized as an industry leader. Commitment to quality is evident in Star’s ISO 9001:2015 certification. Furthermore, Star’s team is always ready to address inquiries and manage project requests, ensuring clients receive services that exceed expectations.
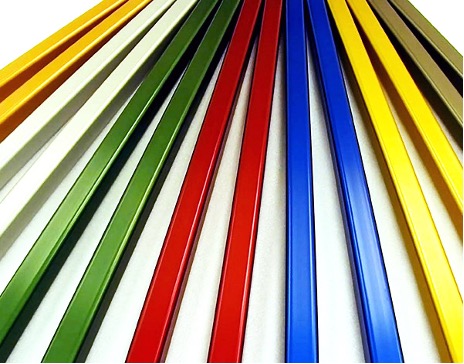
Star Extruded Shapes: State-of-the-Art Facilities and Diverse Capabilities
Operating from a 34,000-square-foot facility, Star offers a complete range of aluminum finishing services, including powder coating, anodizing, and e-coating. From multi-stage pretreatment to infrared boost on cure ovens, our state-of-the-art facility ensures your products receive the highest quality finishes.
Finishing capabilities encompass class 1, 2, and 3 anodized coatings, hard coatings, two-step architectural anodizes, Teflon impregnation, and dry film lubricants. These finishes are not only of superior quality but also comply with RoHS standards. You can rest assured that your products are visually appealing and environmentally friendly.
Custom Solutions and Assembly Expertise
Star Extruded Shapes offers both standard and custom aluminum profiles, catering to a variety of needs. Services include custom aluminum fabrication and complete assembly capabilities, positioning Star as a one-stop-shop for all your needs.
Let’s Connect!
Contact our team today to discuss your project requirements and get a quote. Discover why countless clients choose their exceptional services. Don’t hesitate to contact Star and take the first step towards the success of your project!