Staying Ahead: Key Aluminum Extrusion Trends Shaping 2025
Aluminum extrusion trends are evolving rapidly, shaping industries and driving innovation. Therefore, as we enter a new year, it’s essential to understand what’s fueling these changes and how businesses can stay ahead of the curve.
The aluminum extrusion market is estimated to be worth $64.58 billion in 2025. In fact, it is projected to grow to over $194.89 billion by 2037. Domestic aluminum extruders are expected to produce nearly 7 billion pounds of extruded aluminum by 2025. This surge begs the question: which industries will drive this demand, and what factors make aluminum extrusions indispensable in their applications?
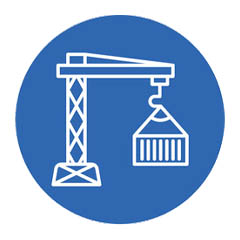
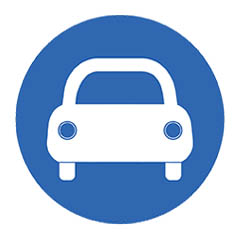
Construction
The construction industry is experiencing a resurgence, driven by the growing demand for residential and commercial buildings. Medical facilities have emerged as a particularly high-growth category. Aluminum extrusions play a critical role in construction applications, including framing, doors, windows, awnings, curtain walls, and more, making the industry a major driver of demand.
Federal highway and infrastructure legislation has further boosted the demand for aluminum extrusions, creating jobs across all 50 states. Related markets, including signage, bridges, and railings, have also benefited, reinforcing the construction industry’s influence on aluminum extrusion trends.
Automotive
Automakers are increasingly utilizing aluminum extrusions to produce vehicles that are lighter, safer, and more environmentally friendly. As the demand for electric vehicles (EVs) grows, aluminum extrusion trends are being shaped by their role in EV battery systems, charging infrastructure, and manufacturing facilities.
The amount of aluminum in each vehicle continues to climb, with a projected net gain of 56 pounds per vehicle between 2020 and 2025. This trend, coupled with the establishment of new manufacturing plants, highlights the increasing reliance on extruded aluminum in the automotive sector, further driving growth within the aluminum extrusion industry.
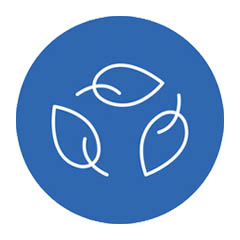
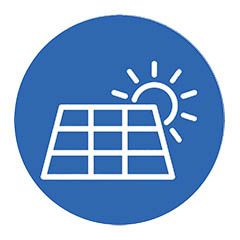
Sustainability
Aluminum is one of the most recycled industrial materials, making it a cornerstone of sustainability efforts. Supported by a robust recycling network in North America, over 90% of aluminum from buildings and vehicles is recycled at the end of its lifecycle. Its unique properties remain unchanged through mechanical processing. This allows extruded aluminum to be recycled repeatedly without degradation.
Aluminum’s infinite recyclability, paired with it’s lightweight nature, high strength-to-weight ratio, corrosion resistance, and formability, positions aluminum extrusions as essential components in countless sustainable solutions. As sustainability continues to shape aluminum extrusion trends, its eco-friendly qualities will drive adoption across industries.
Solar Industry
Aluminum extrusions are a key component in solar panel racking systems. The demand for aluminum is expected to increase as the solar industry grows. The International Renewable Energy Agency (IRENA) estimates that the expected increase in solar capacity globally will lead to an extra global demand of 160 million tons of aluminum by 2050. With these numbers, the solar industry’s share of overall aluminum consumption will leap from 3% to more than 12%. Additionally, campaigns such as “Built in America,” requiring percentage thresholds of U.S. made materials, have unexpectedly added a new wave of solar panel framing into the domestic economy.
Finish Versatility
Aluminum extrusions are inherently versatile, offering natural resistance to environmental stresses thanks to a protective oxide coating that forms upon exposure to the atmosphere. In many cases, this transparent oxide film provides sufficient protection for extruded aluminum applications.
However, when additional surface protection or aesthetic enhancement is needed, aluminum extrusions can be finished in a variety of ways. Options such as painting, anodizing, or mechanical treatments allow for customization, making aluminum extrusions ideal for a wide range of industries and applications. This versatility continues to shape aluminum extrusion trends, driving their adoption in both functional and decorative projects.
How Is Star Extruded Shapes Staying Ahead of The Curve?
Star Extruded Shapes demonstrates a steadfast commitment to quality, innovation, and growth through continuous investments in equipment and technology. This dedication was evident in the installation of a new 4th press in late 2023, the expansion of CNC machine offerings, and ongoing accreditations. Most notably, Star has introduced the TrackScan-P 3D Tracking Scanner by Scantech, a cutting-edge tool that enhances precision and efficiency.
Star’s proactive approach to adopting advanced solutions reflects its commitment to staying at the forefront of aluminum extrusion trends. By aligning with the evolving needs of its clients and the industry, Star remains a trusted leader in extruded aluminum innovation.
Interested In Finding Out More About Star?
Contact the Star team today to discuss your project requirements and receive a tailored quote. Discover why countless clients trust Star for exceptional aluminum extrusion solutions and cutting-edge services. Take the first step toward making your project a success—reach out now!
Follow us on Social Media!
Facebook: https://www.facebook.com/profile.php?id=100063753529991
LinkedIn: https://www.linkedin.com/company/star-extruded-shapes