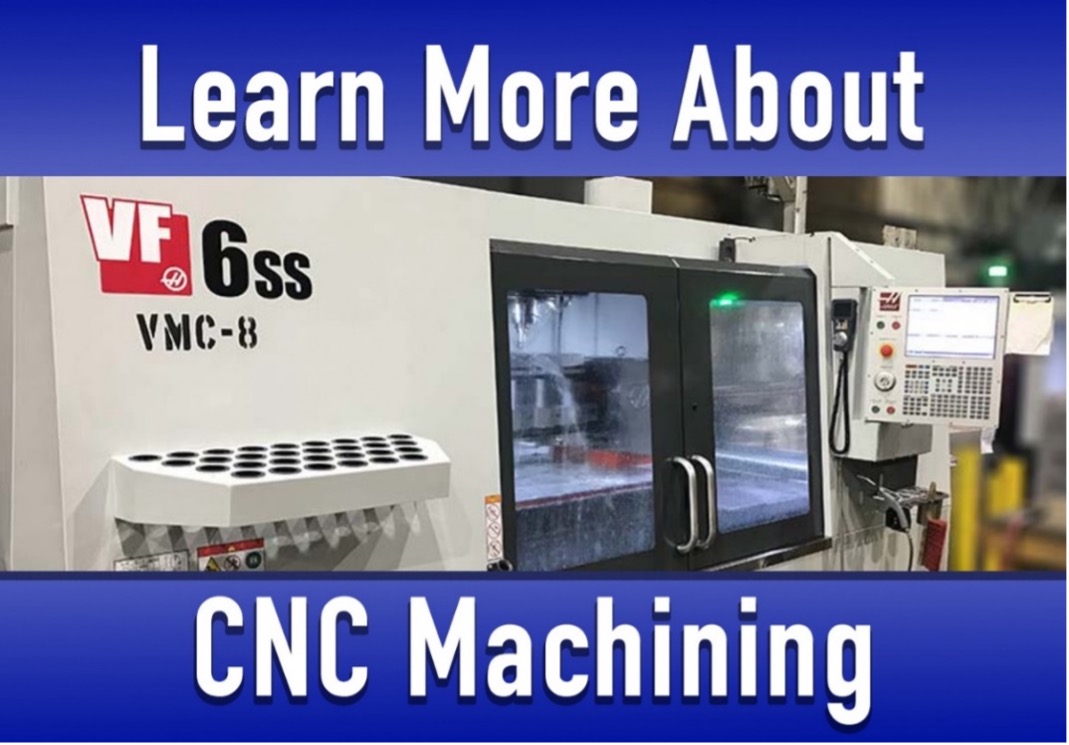
CNC machining has significantly advanced the field of precision manufacturing, and when it comes to working with metals, aluminum stands out for its topnotch qualities. With this guide brought to you by an aluminum extrusion expert, Star Extruded Shapes, we will delve into the nuances of CNC machining aluminum, revealing how this technique is crucial in creating detailed, durable, and lightweight components.
What Does CNC Stand For?
CNC stands for computer numerical control. Computer numerical control (CNC) is an automatic technology that uses a computer program to control mechanical tools. A single tool can perform multiple functions with a custom computer program. Changes and modifications in the outcome are possible with changes in the program without modifying the equipment.
The term ‘numerical’ within CNC indicates the ability of this technology to use numbers for maneuvering the tools. Numbers may refer to coordinates, speeds, degrees, or many other denominations. The machine tools translate these numbers based on the commands in the program. CNC technology has significantly broadened the capabilities of production processes across a myriad of industries, enhancing both efficiency and precision.
How Did CNC Machining Evolve?
The roots of CNC machining can be traced back to the 1940s, marking its inception before the advent of modern computers. Early numerical control systems used the punched tape method as the logic command. The punched tape mechanism operated with mechanical devices called cams. The cams are the very same thing that works a music box or a player piano. While cams provided automation to tools, they could not provide the customization of a computer program. The evolution of numerical control occurred as computing concepts were perfected in the later decades.
What Are the Benefits of Aluminum With CNC?
Aluminum alloys offer varying properties that make them ideal for CNC machining applications. Manufacturers often utilize aluminum for various products because it is inexpensive, non-toxic, recyclable, and machinable. This alloy is also lightweight, durable, ductile, and versatile enough to be utilized in many different applications across a wide range of industries. So, let’s dive into some more of the benefits.
· Strength-to-Weight Ratio
Aluminum is about one-third of steel’s density, making it a relatively light metal. Aluminum exhibits extraordinarily high strength even though it has a low weight. Therefore, this high strength-to-weight ratio makes aluminum ideal for CNC machining.
· Recyclability
CNC machining is a subtractive process that generates a consistent chip load, which is often viewed as waste material. However, aluminum is highly recyclable; as a result, it requires minimal cost, effort, and energy to recycle.
Less waste is produced in the process due to the ability to maximize every usable surface area, when removing the undesired “leftover” aluminum. Furthermore, the recyclability of aluminum makes it a more environmentally friendly metal for machining, making it a more sustainable choice in the manufacturing industry.
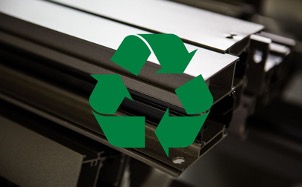
· Machinability
It is easier to form and machine aluminum alloys than other metals. You can use machine tools to cut aluminum easily and quickly, since it is soft and chips easily. This characteristic not only makes CNC machining aluminum more cost-effective but also demands less power during the machining process. A distinct advantage of opting for CNC versus hard tooling (punching or stamping) is lower start-up costs for tooling & fixtures, as well as it being a faster production process.
The excellent machinability of aluminum alloys minimizes deformation risks during machining. This ensures greater precision in crafting custom aluminum parts. CNC machines excel in maintaining tight tolerances effortlessly when machining aluminum, facilitating higher accuracy in the finished products.
· Corrosion Resistance
Aluminum has natural corrosion resistance under various conditions. However, you can anodize your aluminum machined parts to enhance these properties. Also, it would help to understand different aluminum grades have varying levels of corrosion resistance. Despite this variance, the aluminum grades most employed in CNC machining boast outstanding corrosion resistance. This attribute significantly contributes to the durability and longevity of CNC machined aluminum components.
· Electrical Conductivity
Pure aluminum retains electrical conductivity of about 37.7 million Siemens per meter at room temperature. Aluminum alloys provide electrical conductivity for their parts, making them useful for electrical components, even though they may display lower conductivities than pure aluminum.
· Custom Finishing
Aluminum machined parts are compatible with extensive surface finishes such as anodizing, powder coating, and painting to achieve the preferred custom appearance for your project.
How Does a CNC Machine Tool Move?
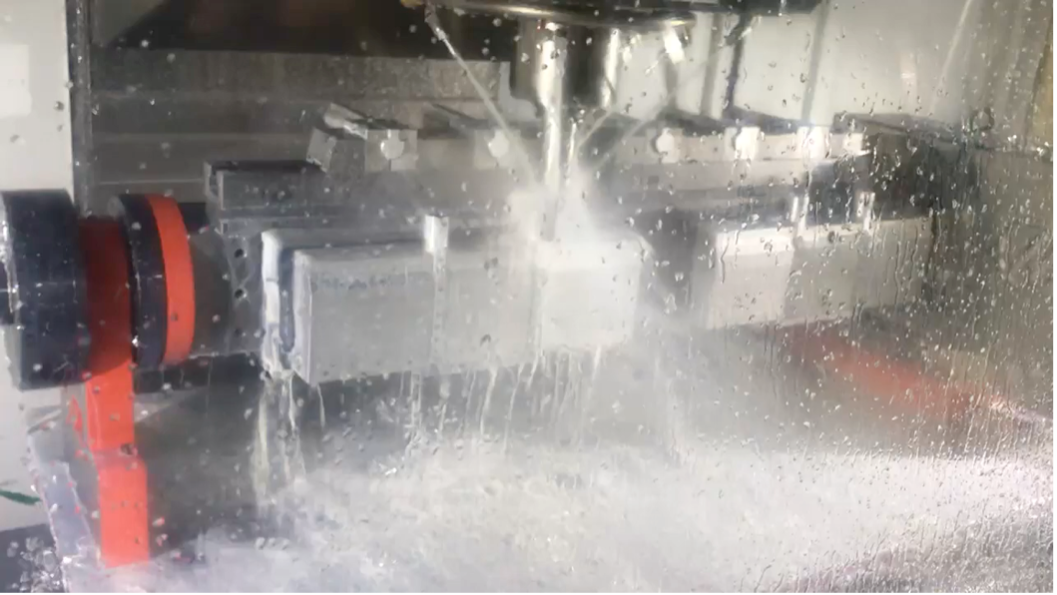
· Rapid Motion
Rapid motion positioning (point interpolation) — In this method, the machine tool moves to its target location via the shortest possible route. The speed of movement is set to maximum, and this positioning system allows for faster production. This approach allows for quicker transitions between machine points, enhancing overall efficiency and reducing manufacturing time.
· Straight Line Motion
Straight-line motion (linear interpolation) — In this method, the machine tools move parallel to X and Y axis without any diagonal traversing. After each positioning, the control system recalibrates and starts the next linear movement. While linear positioning tends to be slower compared to rapid motions, its simplicity in programming makes it a practical choice for many machining operations.
· Circular Motion
The circular positioning system moves the tool in a round manner around a central axis. This positioning is used on round objects such as cylinders or hole punching. This method allows for smooth and continuous motion, enabling the creation of curves and circular shapes with precision
What Kind of Files or Processes Does Star Go Through with The Customer?
The CNC Machining Process
The CNC machining process can be divided into four basic steps:
- Designing your aluminum fabrication project — Whether you come to Star with a full fabrication print or just an idea, we work with you to achieve your fabrication and design requirements. We utilize computer-aided design (CAD) and computer-aided manufacturing (CAM) programs to help create and execute yourfabrication needs.
- Converting the CAD model information and generating a CNC program.
- Performing the initialization or set-up of the CNC machine.
- Running the stored program to perform the machining operation.
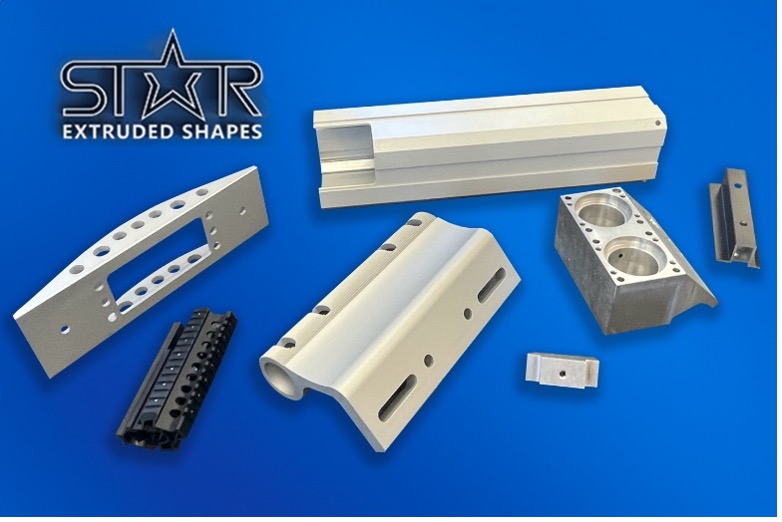
What Does Star Offer with Their CNC Capabilities?
Star offers an array of aluminum extrusion fabrication options. But let’s focus on the CNC offerings. We have thirteen CNC machines that include vertical and horizontal machining. Our team of aluminum extrusion expert reviews each project in-depth, validates manufacturability and ensures your parts are processed with maximum efficiency without compromising quality.
Star’s thirteen CNC machines also have 4th-axis capabilities. 4th-axis machining offers capabilities like 3rd-axis, but with additional rotary movement around the X-axis. This allows us to mill aluminum extrusions on multiple axes without having to change tooling, which increases productivity, as mentioned earlier.
Do you still have questions or want to explore how we can help you execute your idea?
Star is a one-stop shop for all things aluminum extrusion and supporting services. Our commitment to excellence is reflected in our promise to provide competitively priced, high-quality aluminum extrusions, delivered precisely when you need them. Our passion for transforming your concepts into tangible successes is driven by our superior design and manufacturing prowess.
Let’s Connect!
Contact our team today to discuss your project requirements and get a quote. Discover why countless clients choose our exceptional services. Don’t hesitate to contact us and take the first step towards the success of your project
Facebook: https://www.facebook.com/profile.php?id=100063753529991
LinkedIn: https://www.linkedin.com/company/star-extruded-shapes